Is It Safe to Continue Business During Mold Remediation on Your Property?
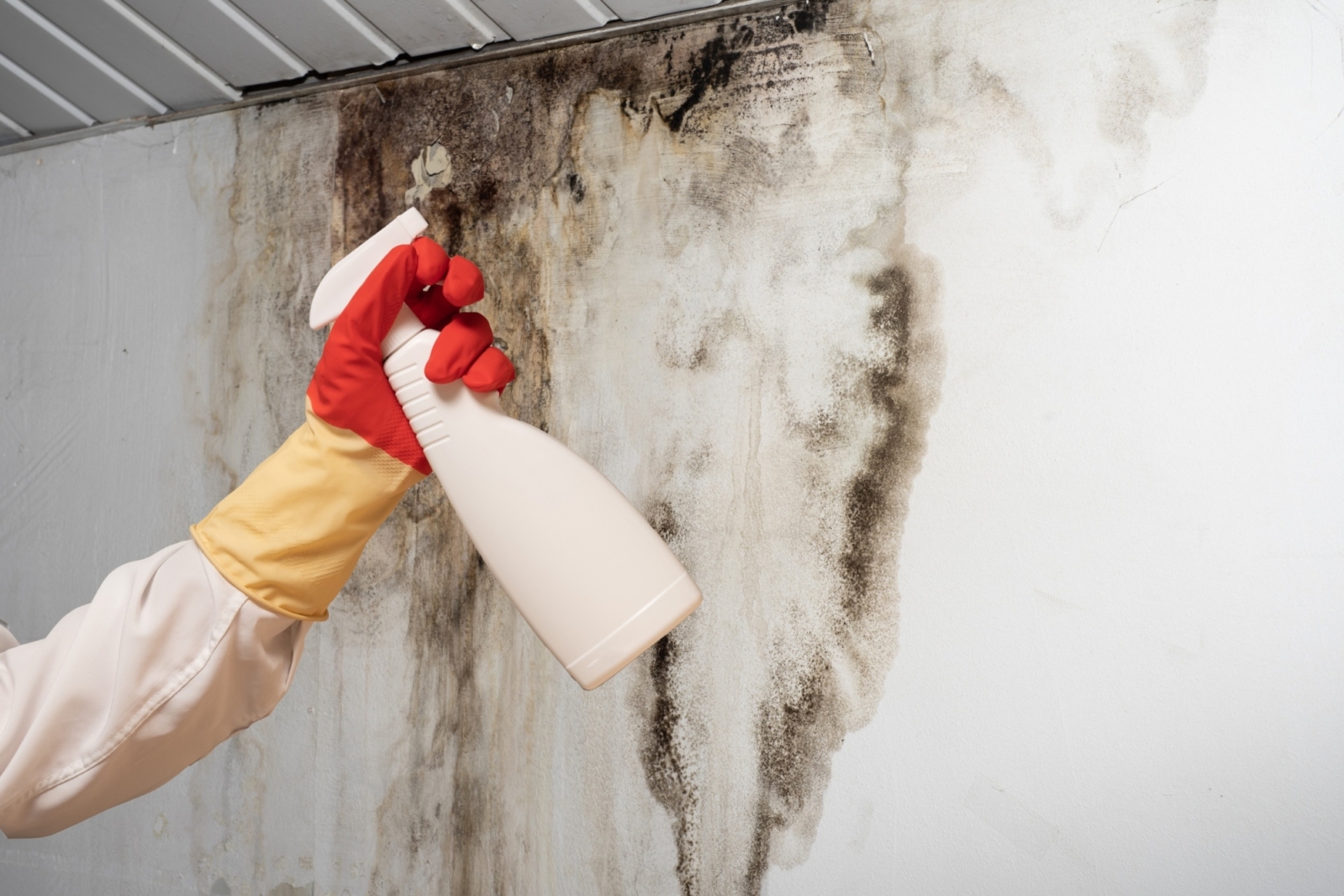
Mold can be challenging to any business, not only impacting the physical structure of a building but also the health and safety of employees and customers alike. When mold is discovered, prompt and effective remediation is imperative. The question asked among business owners is whether it's safe to continue operations during the mold remediation process or is it necessary for the business owner to close the property entirely until the mold issue is resolved. In this blog, we will explore the risks, considerations, and best practices for maintaining business continuity during mold remediation. We aim to help you understand and explore your options should your encounter mold or water damage on your property.
Understanding the Risks of Mold Exposure
Mold exposure can cause a variety of health problems, particularly for individuals with respiratory conditions, allergies, or weakened immune systems. Common symptoms may include the following:
Respiratory Issues: Coughing, wheezing, and difficulty breathing.
Allergic Reactions: Sneezing, runny nose, and itchy eyes.
Skin Irritation: Rashes or hives.
Chronic Conditions: Prolonged exposure can lead to more serious conditions like asthma attacks or lung infections.
Given these risks, it's essential to carefully evaluate each unique situation as a business owner before deciding to keep your business open during mold remediation.
Factors to Consider
Several factors influence whether it’s safe to continue business operations during a mold remediation process:
Extent of Mold Infestation-Localized vs. Widespread: If mold is confined to a small, isolated area, it may be possible to continue operations with minimal disruption. However, widespread mold contamination can pose significant health risks and may require temporary closure.
Type of Mold-Toxic vs. Non-Toxic: Certain types of mold, such black mold, formally known as Stachybotrys chartarum, produce mycotoxins that are particularly harmful to health. The presence of toxic mold may necessitate more strict, immediate safety measures or even temporary closure.
Remediation Process-Containment Measures: Effective containment strategies can prevent mold spores from spreading to unaffected areas, reducing health risks. Negative air pressure machines and physical barriers can help maintain a safe environment.
Employee and Customer Health-Vulnerable Individuals: Consider the health of employees and customers. Those with preexisting conditions may be more susceptible to mold-related illnesses and may need to be temporarily relocated. This one is tricky because you really don’t know the health of a customer entering your facility.
Regulatory Compliance-Health and Safety Regulations: Adhering to local health and safety regulations is critical. Non-compliance can result in fines or legal action, in addition to compromising the well-being of your staff and customers.
Best Practices for Continuing Business Operations
If you decide to keep your business open during mold remediation, implementing best practices is crucial to ensure safety and minimize disruption.
1. Effective Communication
Transparency: Keep employees and customers informed about the situation, the steps being taken, and any potential risks. Transparency fosters trust and cooperation.
Signage: Clearly mark the areas under remediation and provide alternative routes if necessary.
2. Containment Strategies
Physical Barriers: Use plastic sheeting and other materials to create physical barriers around the affected areas.
Negative Air Pressure: Utilize negative air pressure machines to prevent mold spores from spreading to other parts of the building.
3. Personal Protective Equipment (PPE)
Protective Gear: Ensure that remediation workers and potentially exposed employees wear appropriate PPE, such as masks, gloves, and coveralls.
4. Air Quality Monitoring
Regular Testing: Conduct air quality tests before, during, and after remediation to ensure that mold spore levels remain safe.
HEPA Filtration: Use HEPA air purifiers to remove mold spores and improve indoor air quality.
5. Work Adjustments
Remote Work: Allow employees to work from home if possible, particularly those with health vulnerabilities.
Flexible Hours: Implement flexible working hours to reduce the number of people in the building at any given time.
6. Cleaning and Disinfection
Regular Cleaning: Increase the frequency of cleaning in unaffected areas to prevent mold spores from settling and growing.
Disinfection Protocols: Use mold-killing disinfectants to clean surfaces and reduce the risk of recontamination.
When Temporary Closure Is Necessary
In some cases, continuing business operations during mold remediation may not be feasible or safe. Temporary closure can be a strategic decision to ensure thorough remediation and protect health.
1. Severe Contamination
Extensive Infestation: If mold contamination is extensive, a temporary closure allows for comprehensive remediation without exposing employees and customers to health risks.
2. Health Prioritization
Vulnerable Individuals: Prioritizing the health of employees and customers, especially those with underlying health conditions, may necessitate a temporary shutdown.
3. Regulatory Requirements
Compliance: Adhering to health and safety regulations may require temporary closure to avoid legal repercussions and ensure a safe environment.
Preparing for Business Continuity Post-Remediation
Once mold remediation is complete, preparing for business continuity is essential to prevent future mold issues and ensure a smooth transition back to normal operations.
1. Thorough Inspection
Final Assessment: Conduct a thorough inspection to ensure that all mold has been effectively removed and that the property is safe for occupancy.
2. Preventative Measures
Moisture Control: Address any underlying moisture issues that contributed to mold growth, such as leaks or inadequate ventilation.
Regular Maintenance: Implement regular maintenance and inspections to detect and address potential mold issues early.
3. Employee Training
Awareness: Educate employees about mold prevention strategies and the importance of maintaining a dry, well-ventilated environment.
4. Clearance Testing
Air Quality: Perform clearance testing to confirm that mold spore levels are within safe limits before resuming full operations.
5. Ongoing Monitoring
Routine Checks: Establish a schedule for routine air quality checks and mold inspections to ensure a healthy work environment.
Mold remediation in a commercial property presents significant challenges, but with careful planning and implementation of best practices, it is possible to maintain business operations safely. Evaluating the extent of contamination, type of mold, and health risks, alongside implementing robust containment and communication strategies, can help ensure the well-being of employees and customers. In cases where temporary closure is necessary, prioritize health and regulatory compliance to facilitate thorough remediation. Post-remediation, proactive measures and regular monitoring will safeguard against future mold issues, ensuring a safe and healthy business environment.
Why Should You Join NDS PRIME™?
Effective business planning includes preparing for emergencies and natural disasters. With NDS PRIME™, you can safeguard your business from unexpected disruptions and revenue loss. Our program ensures you’re ready for any situation with:
24/7/365 Emergency Response: Immediate assistance whenever you need it.
Pre-Loss Planning: Strategically prepare to minimize risks and streamline recovery.
Post-Loss Reconstruction: Expert services to restore your property and operations.
Insurance Coordination: Seamless collaboration with major insurance companies.
Mold Remediation Expertise: Tackle mold issues in commercial properties with best practices.
Join NDS PRIME™ for peace of mind and resilience in the face of adversity. Contact us today to start effective mold remediation and gain peace of mind.